Objectif : réduction des consommations d’énergie
La diminution des émissions de Gaz à Effet de Serre dans l’industrie passe par la réduction des consommations d’énergie, et ce grâce à la mise en place d’actions d’efficacité énergétique. La R&D d'EDF développe des outils d’audit et d’optimisation des consommations et de gain de performance, et accompagne les industriels pour mettre en place des projets d’économie circulaire au sein de territoires industriels.
Projet « Usine décarbonée 4.0 » : diagnostiquer la performance énergétique globale pour l’optimiser
EDF accompagne ses clients industriels en leur proposant un diagnostic de leur performance industrielle via plusieurs outils développés par la R&D d’EDF. Rencontre avec Aurélie Kaemmerlen, chef de projet « Usine décarbonée 4.0 ».
« Dans une activité industrielle, la baisse d’émission de CO2 fait partie d’un tout. On ne peut l’envisager indépendamment d’un gain de performance, explique Aurélie Kaemmerlen, chef de projet Usine décarbonée 4.0 chez EDF R&D. Nous accompagnons beaucoup de clients dans cette démarche ». Cette optimisation énergétique et environnementale peut se faire à plusieurs niveaux, en étant accompagné par EDF.
Analyser ses performances
EDF propose, depuis 2019, à ses clients un accompagnement vers la performance industrielle 4.0 nommé « Sprint factory », à l’image d’un sprinteur qui doit avoir un environnement le plus favorable possible pour donner le meilleur de lui-même. « Nous apportons un regard extérieur, expert, sur l’ensemble des données liées à l’activité industrielle. Cette intervention, totalement sécurisée au niveau du recueil des données, permet d’analyser très finement où sont les gains de performance possibles et comment les coupler à une orientation vers des solutions moins énergivores et moins émettrices de carbone », souligne Aurélie Kaemmerlen. Cette offre est désormais intégrée dans l’accompagnement client du Groupe vers la neutralité carbone.
L’offre Motorboard, commercialisée depuis 2021, permet le diagnostic d’un parc de moteurs électriques, qu’il s’agisse des moteurs liés à l’activité industrielle elle-même ou des moteurs dans les installations tertiaires. Cet audit ponctuel s’effectue à l’aide de wattmètres designés dans nos laboratoires et dont les mesures sont analysées par un logiciel reposant sur l’expertise de la R&D pour déterminer automatiquement les optimisations possibles. À l’issue de l’audit, l’industriel connaît mieux l’utilisation et le coût de son parc moteur ainsi que les solutions éco-efficaces adaptées pour optimiser son parc. « Nous développons actuellement des options complémentaires de suivi dans le temps et de maintenance prédictive » précise Aurélie Kaemmerlen.
Améliorer la régulation en milieu industriel
L’efficacité énergétique et la performance industrielle peuvent également être améliorées grâce à une meilleure régulation des équipements industriels. En effet, un contrôle commande non optimisé ou mal réglé peut engendrer des surconsommations notables. La R&D d’EDF a donc mis au point la solution EAC (Easy Advanced Control) qui permet d’accéder à des régulations très performantes tout en restant simple d’utilisation grâce à une loi de commande d’automatisme brevetée. « Nous achevons les premiers déploiement clients et nous commercialiserons ce service dans les prochains mois pour rendre accessibles aux techniciens et opérateurs de maintenance des commandes avancées, sans formation spécifique », précise Aurélie Kaemmerlen.
D’autres innovations dans les cartons
La R&D travaille actuellement sur un système de diffusion d’air très innovant (réversible chaud/froid) qui va améliorer les conditions au poste de travail des salariés dans les usines tout en réduisant les consommations d’énergie. Des industriels ont déjà montré leur intérêt pour ce concept.
Démarche EPIFLEX : décarboner en créant des symbioses industrielles
Une partie des 80 millions de tonnes d’équivalent CO2 émises par les industriels français chaque année peut être supprimée en s’organisant entre entreprises, les « déchets » de l’une devenant une ressource pour l’autre. Rencontre avec Solène Le Bourdiec, qui dirige le projet EcoCirT au sein de la R&D d’EDF dans lequel a été développée la démarche d’économie circulaire EPIFLEX.
« EPIFLEX est une démarche à part entière, qui s’appuie sur un ensemble d’outils et méthodologies en vue de mettre en place des projets collaboratifs entre entreprises de manière optimisée, souligne Solène Le Bourdiec. Grâce à des outils spécifiques, dont le logiciel innovant PHOENIX, et après 10 ans de travail sur ces questions, nous sommes en mesure de fournir une assistance à la mise en place d’économie circulaire via l’installation de boucles locales d’énergie et de matière sur les territoires, en garantissant la faisabilité technique et la rentabilité économique ».
Modéliser pour optimiser
L’économie circulaire à l’échelle d’un groupe d’entreprises installées sur un même territoire consiste à réutiliser certains flux sortants d’un site industriel pour en faire une ressource pour un autre. Il peut s’agir de flux de chaleur, d’eaux usées, d’hydrogène ou encore de toutes sortes de matières, comme des palettes de bois par exemple : nombreuses sont les sources d’économie possible si on se sert de ces produits perdus pour en faire une ressource dans le cadre de l’activité d’un industriel voisin. « La complexité est donc d’optimiser les différents échanges possibles en fonction des partenaires potentiels présents pour opter pour les meilleures solutions techniques acceptables économiquement pas les acteurs », explique la cheffe de projet.
10 années de R&D pour une démarche alliant outils et savoir-faire
Cette optimisation peut s’avérer complexe quand il s’agit de coordonner plusieurs entreprises industrielles et l’ensemble de leurs flux entrants et sortants. C’est pourtant ce qui a été fait entre 20 sites industriels de la zone industrialo-portuaire de Dunkerque, sous la direction de la R&D d’EDF, dans le cadre du projet EPIFLEX soutenu par l’ADEME entre 2018 et 2021, en partenariat avec les Mines ParisTech.
« Dans ce type de projet, les outils d’optimisation sont primordiaux pour proposer les bonnes options techniques et s’assurer de la rentabilité des investissements associés, mais ils ne font pas tout, souligne Solène Le Bourdiec. C’est un travail de co-construction avec les acteurs industriels, la collectivité et les associations locales intégrés à la démarche. Mon rôle a été d’animer le comité de pilotage pour donner vie au projet et de proposer différents choix techniques viables en me basant sur nos calculs d’optimisation ».
Résultat : il y est possible d’économiser plus de 1,5 million de m3 d’eau par an et de fortement décarboner le territoire en évitant l’émission de 43 kt de CO2 chaque année.
« Les contours du projet dunkerquois sont désormais définis et ce projet est une vitrine formidable pour l’économie circulaire. Il nous reste à le concrétiser, en aidant à la mise en place de modèles économiques durables et à trouver des financements, ce qui est aussi un des savoir-faire d’EDF ».
Et ensuite ?
« L’intérêt de ce type d’initiative est d’être dupliquée, multipliée. Nous sommes à l’écoute de nouveaux territoires, pour faire la modélisation de leurs flux spécifiques en fonction des problématiques et des données des industriels. »
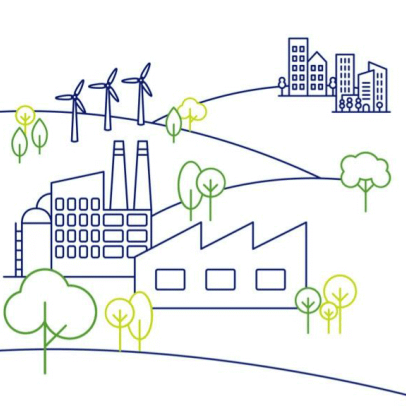
Portrait
Solène Le Bourdiec, spécialiste de la simulation numérique
« J’aime confronter la théorie à la réalité et aux besoins des clients. »
« Je suis ravie que l’électrification des fours revienne sur le devant de la scène ! »
Ingénieur-chercheur à la R&D d’EDF, Marianne Le Boulch a travaillé en tant qu’experte du chauffage industriel pendant 15 ans jusqu’en 2009. Fort de ses connaissances, elle a ensuite accompagné les commerciaux de l’entreprise et leurs clients dans des opérations d’efficacité énergétique. Depuis janvier 2022, elle revient à son sujet de prédilection pour accompagner les entreprises dans une démarche d’électrification, synonyme de décarbonation.
Quel est votre parcours ?
Dès mon arrivée à la R&D d’EDF, en 1994, j’ai travaillé en tant qu’experte du chauffage des solides par des moyens électriques : je réalisais des expertises sur les procédés industriels et je développais des solutions innovantes. En 2009, je suis devenue chef de projet pour l’appui aux clients grand compte : il s’agissait là d’accompagner les clients dans leurs projets d’efficacité énergétique et d’améliorer la compétitivité de leur activité.
Consommer moins est une préoccupation très présente chez les industriels, soucieux de diminuer leurs coûts de production. Mais les modifications majeures de leurs procédés sont cycliques car elles sont liées aux politiques et aux prix des énergies. Depuis mi-2020 et les annonces du plan de relance, on vit une formidable accélération ce qui nous a amené à étudier plusieurs dizaines de projets de décarbonation chez les industriels français.
L’un des leviers de la décarbonation de l’industrie est l’adoption de fours électriques. Je suis donc revenue à ce sujet que je connais bien et, depuis janvier 2022, je suis responsable du projet Électrification et fours industriels.
Quels sont vos objectifs ?
À titre personnel, je reviens sur un sujet connu mais où beaucoup de choses ont changé en 13 ans. Je suis ravie que l’électrification des fours revienne sur le devant de la scène ! Je redécouvre un domaine où il est devenu plus simple de répondre aux besoins des clients car les possibilités sont devenues plus nombreuses : il est généralement tout à fait possible de substituer un four à gaz par un four électrique. Néanmoins, les spécificités des activités industrielles requièrent une expertise : l’accompagnement d’EDF R&D permet aux industriels de franchir le pas en faisant le meilleur choix entre les différentes technologies existantes. Four à résistance ? À induction ? Infrarouge ? Micro-ondes ? Mixte ? Nous connaissons les particularités de chaque solution et nous sommes en mesure de les conseiller efficacement.
Quels sont les secteurs industriels les plus concernés par l’électrification des fours ?
En fait, tous les secteurs sont concernés ! Parmi les principaux, on peut mentionner le secteur des métaux avec le besoin de décarboner la sidérurgie ou avec le besoin de matériaux de construction (verre et ciment décarbonés) pour répondre à la nouvelle règlementation RE2020.
Le secteur agroalimentaire n’est pas en reste avec l’attente des consommateurs de produit respectueux de l’environnement où la diffusion des technologies - résistance, induction voire micro-ondes - ont de beaux jours devant eux. La R&D d’EDF a l’ambition de travailler avec les fabricants de fours électriques et des industriels afin de faire évoluer les solutions techniques pour qu’elles soient à la fois adaptées aux procédés et flexibles pour s’inscrire dans un système électrique avec plus d’ENR intermittentes.
En tant que chercheur, j’ai beaucoup de plaisir à travailler sur ces projets car ils obligent à se confronter au monde réel et à prendre une part active dans l’évolution de l’industrie vers moins d’émissions de CO2 !
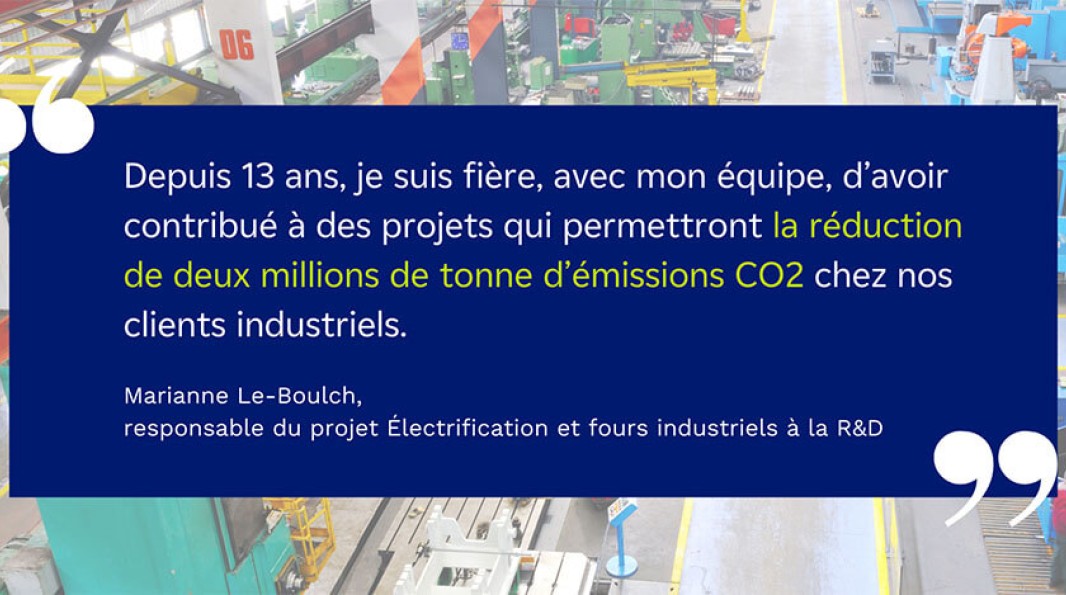