Stop aux énergies fossiles !
La substitution des énergies fossiles, fortement émettrices de gaz à effet de serre, par des énergies bas carbone, telle que l’électricité, reste le levier le plus efficace pour décarboner l’industrie.
En effet l’électrification peut jouer un rôle majeur dans la décarbonation de ce secteur, dès aujourd’hui grâce à une plus grande diffusion de technologies déjà disponibles, et demain grâce à des ruptures technologiques et culturelles.
L’électrification peut permettre de réduire jusqu’à 50 % les émissions de l’industrie (vision maximale). Elle constitue un levier efficace pour diminuer le recours aux autres solutions de décarbonation de l’industrie, dont le potentiel est contraint.
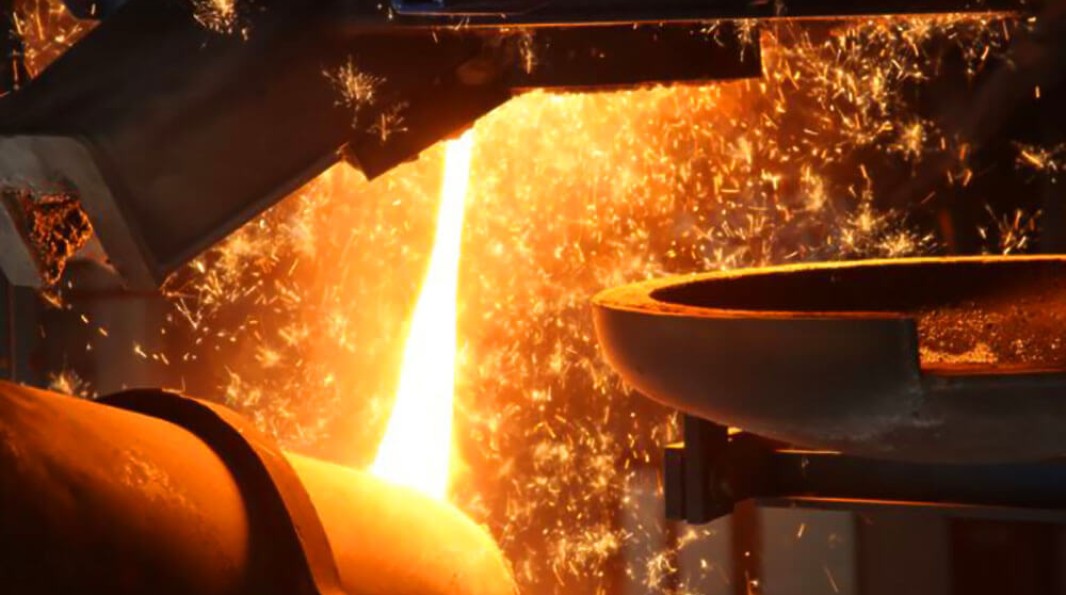
Décarboner la production d’acier via l’électrification
La production d’acier est responsable de 5,7 % des émissions de GES(1) en Europe(2). En participant au projet européen Siderwin, la R&D d’EDF apporte son savoir-faire et ses compétences pour décarboner la production d’acier, comme l’explique Matthildi Apostolou, ingénieur-chercheur impliquée dans ce projet.
« Le procédé actuel de production d’acier primaire est extrêmement émetteur de CO2 par son utilisation intensive de charbon : environ deux tonnes de CO2 sont émises pour chaque tonne d'acier produite. En effet, pour produire de l’acier il faut extraire l’oxygène des atomes de fer : ce procédé est réalisé dans un haut fourneau, ou le minerai de fer (oxyde de fer généralement en petites billes) est réduit en métal par le carbone contenu dans le coke (obtenu par du charbon) », explique Matthildi Apostolou. Décarboner la production d’acier est tout l’enjeu du projet Siderwin, piloté par Arcelor Mittal dans le cadre du programme européen H2020 et réunissant douze partenaires sur 5 ans.
Un procédé révolutionnaire
« Décarboner la production d’acier est un passage obligé pour atteindre l’objectif de neutralité carbone de l’Union européenne d’ici 2050 poursuit Matthildi Apostolou. Siderwin vise à développer un procédé électrochimique permettant de décomposer, par électrolyse, les oxydes de fer en plaques métalliques et en oxygène gazeux. En substituant le charbon par l’électricité, cette technologie innovante permet de réduire de 87 % les émissions directes de CO2 de la filière ».
Néanmoins, son adoption par les aciéries nécessite une adaptation en amont pour l’alimentation du procédé en électricité, et des modifications en aval de la production elle-même : alors que les hauts fourneaux actuels produisent de l’acier liquide, Siderwin mène à la production des plaques d’acier solide qui nécessiteront donc d’être fondues ensuite.
Pour modifier le processus de formation de l’acier, il faut donc réinventer la production. Au-delà d’investissements importants dont il faut démontrer la pertinence et la viabilité économique, cela signifie aussi que les vecteurs énergétiques que sont le charbon et le gaz sont remplacés par l’électricité. Les ingénieurs-chercheurs de la R&D d’EDF sont intervenus dès le départ du projet dans la modélisation du système électrique européen et la scénarisation des mix de production électriques permettant de satisfaire une demande supplémentaire allant jusqu’à 471 TWh électriques à l’échelle européenne dans le cas de la substitution complète du parc des hauts fourneaux actuels par siderwin d’ici 2050.
Un premier pilote aux bancs d’essais
Les partenaires du projet Siderwin ont conçu et construit un pilote permettant la production de plaques d’acier de 100 kg sur le site de Arcelor à Maizières. Les premiers essais ont démarré en décembre 2021 et se poursuivront en 2022/2023.
« C’est un enjeu de taille car la métallurgie est une grande consommatrice d’énergie. En optant pour des procédés électriques innovants il devient possible de réduire drastiquement les émissions de CO2 du secteur. Nous devons donc être à même d’étudier, par une modélisation détaillée du système électrique européen, différents scénarios permettant d’évaluer différents mix de production d’électricité décarboné pour répondre à cette demande supplémentaire d’électricité ainsi que d’évaluer la flexibilité apportée au réseau via des scénarios d’effacement », conclut Matthildi Apostolou.
(1) GES : gaz à effet de serre.
(2) La production d’acier est responsable de 4 % des émissions de GES en France et 5.7 % des émissions de GES en Europe (source : developpement-durable.gouv.fr, données 2019 en Mt CO2 équivalent & ec.europa.eu/info/sites/groupe/files/swd-competitive-clean-european-steel_en.pdf)
Pour plus d’informations : www.siderwin-spire.eu
PAC-HT : un projet de pompes à chaleur décarbonées jusque 150 °C
Une part importante de l’énergie consommée par l’industrie est utilisée sous forme de chaleur au sein de différents procédés tels que le séchage, la stérilisation, le traitement des matériaux, la distillation… Comment décarboner ce vecteur très énergivore et trop souvent très émetteur de CO2 ? Rencontre avec Clément Gachot en charge d’un projet qui vise au développement pour la R&D d’EDF des pompes à chaleur innovantes, adaptées aux procédés industriels.
« Les pompes à chaleur sont pour l’instant très minoritaires dans l’industrie notamment dès lors qu’il s’agit de dépasser 80 °C. Or dans la gamme 80-150 °C se trouvent une part importante des besoins industriels et les pompes à chaleur y sont rentables, efficaces, moins émettrices de carbone que des chaudières à gaz ou fioul et permettent d’utiliser la chaleur fatale disponible qui représente environ la moitié de l’énergie thermique consommée sur les sites industriels », constate Clément Gachot, chef du projet « Solution de production et distribution de chaleur et de froid Bas Carbone » (SoBasCarbone) à la R&D d’EDF. Un constat qui a conduit l’équipe projet à développer en partenariat avec des industriels fabricants de nouvelles pompes à chaleur hautes températures, capables d’atteindre jusqu’à 150 °C.
Des opportunités massives avec des contraintes industrielles multiples à lever
« Le dernier rapport de l’Agence Internationale de l’Energie (AIE) visant la neutralité carbone mondiale à l’horizon 2050 montre que si nous souhaitons tenir cet objectif il faudrait déployer, dans l’industrie légère et à l’échelle mondiale, 500 PAC par mois pendant les 30 prochaines années. En effet, en plus d’être une grande opportunité pour le Groupe EDF, remplacer les chaudières à gaz ou fioul par des dispositifs électriques et plus particulièrement les PAC est un moyen extrêmement efficace de décarboner l’industrie grâce à des coefficients de performance (COP) des pompes à chaleur observés en laboratoire en conditions réelles d’exploitation compris entre 3 et 5 en fonction des cas », explique le chef de projet. En effet, les pompes à chaleur – qui commencent par prélever la chaleur fatale disponible et la transfèrent au flux que l’on veut chauffer - permettent par exemple de produire 1 MWh thermique à partir de 250 kWh d’énergie électrique plus 750 kWh de chaleur fatale récupérée gratuitement.
Comment expliquer alors que les industriels ne les adoptent pas massivement ?
Il y a plusieurs raisons à cela selon Clément Gachot : « Tout d’abord parce que les temps de retour sur investissement sont considérés comme trop longs pour des industriels qui restent prudents dans leur choix d’investissement. Ensuite, les procédés en place utilisent des chaudières avec des circuits historiquement dimensionnés en conséquence. Changer de moyen de production et récupérer la chaleur fatale implique donc un investissement conséquent qui entre dans le bilan économique global de l’opération. De plus, pour les hautes températures (>80 °C), les fabricants de machines proposent peu, voire pas de solution notamment pour produire des besoins à des température au-dessus de 120 °C. Enfin, les industriels ont l’habitude d’utiliser un vecteur énergétique efficace pour leur procédé : la vapeur, et force est de constater que la plupart des pompes à chaleur du marché utilisent le vecteur eau liquide ou air. Nous devons donc intensifier nos collaborations et partenariats avec les fabricants pour proposer des pompes à chaleur adaptées aux besoins des industriels, appuyer nos entités afin de proposer des projets compétitifs aux clients et accompagner, notamment Dalkia, dans la garantie dans le temps de la performance énergétique promises ». C’est le triple objectif poursuivi par le projet « SoBasCarbone » le tout afin d’atteindre l’objectif vertueux d’un avenir neutre en CO2.
Découvrez en vidéo le laboratoire PAC HT
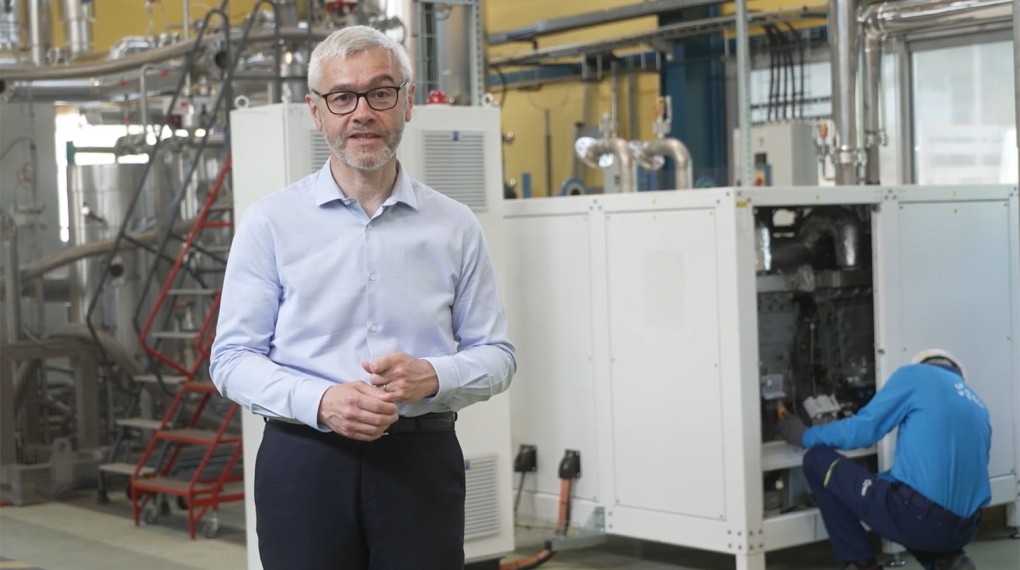
Votre navigateur ne prend pas en compte le javascript.
Pour vous permettre d'accéder à l'information, nous vous proposons de consulter la vidéo dans un nouvel onglet.
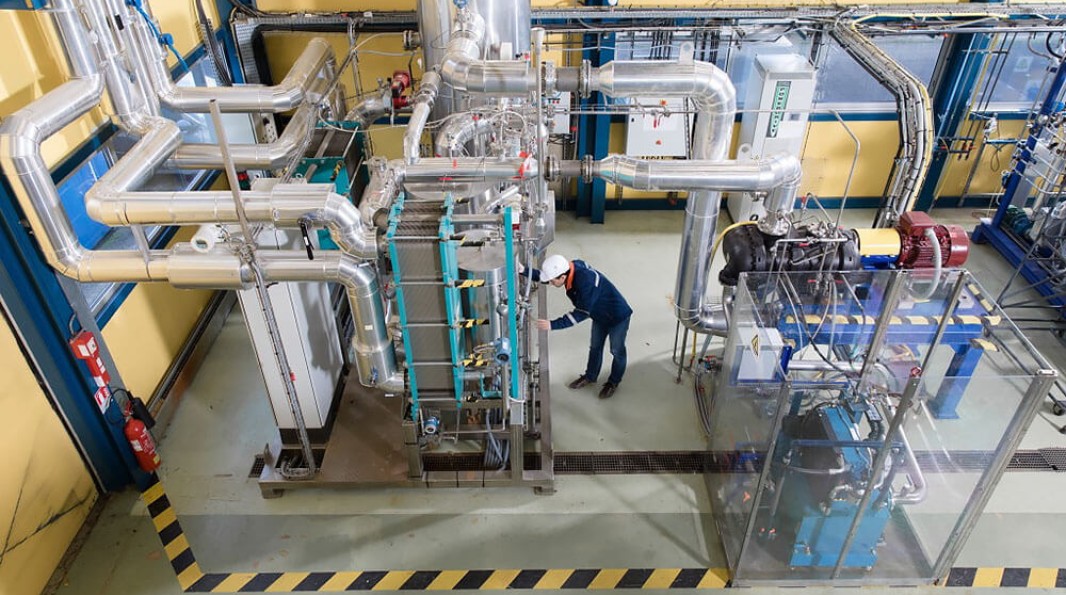
Le laboratoire et les technologies développées par le Groupe EDF
La R&D travaille depuis de nombreuses années aux développements de prototypes de PAC HT répondant aux attentes de l’industrie dans son laboratoire dédié sur le site EDF Lab les Renardières (77). Certaines ont déjà été déployées sur des sites industriels et d’autres le seront prochainement. En effet, TRANSPAC, un concept performant et unique de PAC en cycle transcritique permettant notamment d’améliorer considérablement le COP et de réchauffer de l’air à 140 °C verra son premier prototype à l’échelle 1 déployé en collaboration avec Dalkia dans l’industrie papetière sur un procédé de séchage. Aussi, PACO, un concept innovant de PAC HT fonctionnant avec le cycle thermodynamique de l’eau afin de répondre à la problématique des fluides frigorigènes (inflammabilité, impact sur l’ozone…) et permettant de produire de l’eau chaude ou de la vapeur à 130 °C a été développée en collaboration avec un Johnson Controls Industries et pourra être déployé par exemple sur des procédés de distillation. Enfin, la R&D d’EDF développe, notamment via le projet Européen Bamboo, un concept de PAC productrice de vapeur, une première démonstration en laboratoire est prévue en 2022.
Hydrogène décarboné, une solution pour la chimie et la sidérurgie
L’hydrogène est un formidable vecteur énergétique et pourrait contribuer à la transition énergétique mais à la condition que sa production soit décarbonée.
Actuellement l’hydrogène est utilisé principalement dans l’industrie pour la production d’ammoniaque, d’engrais, pour la chimie ou encore le raffinage. Il est également utilisé comme vecteur d'énergie dans le domaine spatial et la mobilité.
Avec près d’un million de tonnes d’hydrogène produit en France et par an, la décarbonation de son usage est devenu une priorité pour la transition énergétique, à condition de rester compétitif dans ses secteurs d’usage.
Aujourd'hui, 96 % de la production mondiale d'hydrogène est réalisée à partir d'énergies fossiles, un procédé fortement émetteur de gaz à effet de serre (environ 10 kg émis pour 1 kg d'hydrogène produit). Cependant des procédés de fabrication de l'hydrogène de façon décarbonée existent, par électrolyse de l'eau grâce à de l'électricité bas carbone (ENR et nucléaire) par exemple.
Ce sont ces procédés de fabrication qui vont permettre de faire de l'hydrogène un élément clé de la transition énergétique pour décarboner les deux pans de l'économie les plus émetteurs de CO2 : l'industrie et les transports.
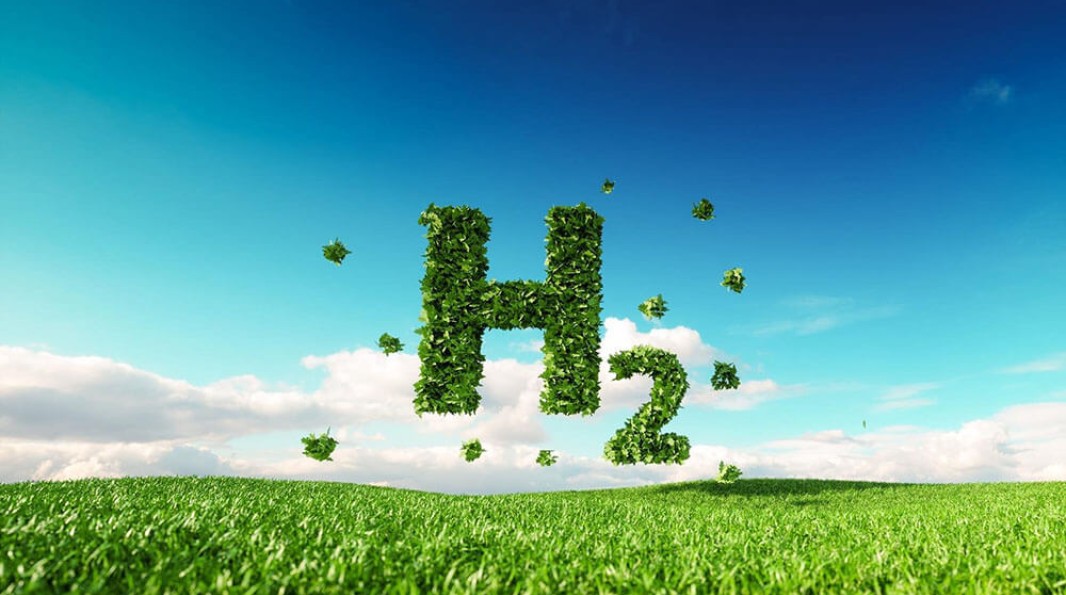