La fabrication additive au service de la maintenance et de la sûreté des installations
En plein essor dans l'industrie, la fabrication additive plus communément appelée impression 3D regroupe toute une famille de nouveaux procédés de fabrication. Une vraie révolution des modes de production, dont s'est emparée la R&D d'EDF pour répondre aux enjeux de maintenance et de disponibilité des installations du groupe, via la fabrication - ou la réparation - de composants de qualité, dans des délais maîtrisés.
L'actualité récente et les nombreuses initiatives d'impression 3D de visières ou d'embouts de respirateurs dans le cadre de la crise sanitaire ont mis en lumière la rapidité et l'agilité de ces nouveaux procédés de fabrication. Nouveau ? « Pas tout à fait, rétorque Yang Shen, pilote du projet PROFI consacré aux PROcédés de Fabrication Innovants à la R&D d'EDF. Cela fait une petite dizaine d'années que la fabrication additive a fait son entrée dans le secteur aéronautique. Aujourd'hui, la technologie gagne les autres secteurs industriels. » Mais de quoi s'agit-il exactementé ? D'un procédé qui consiste à fabriquer des pièces modélisées sur ordinateur par ajout de couches successives de matière, à l'inverse des procédés d'usinage classiques où l'on enlève de la matière pour atteindre la forme désirée. Il peut être utilisé pour la fabrication de pièces métalliques, plastique ou céramique.
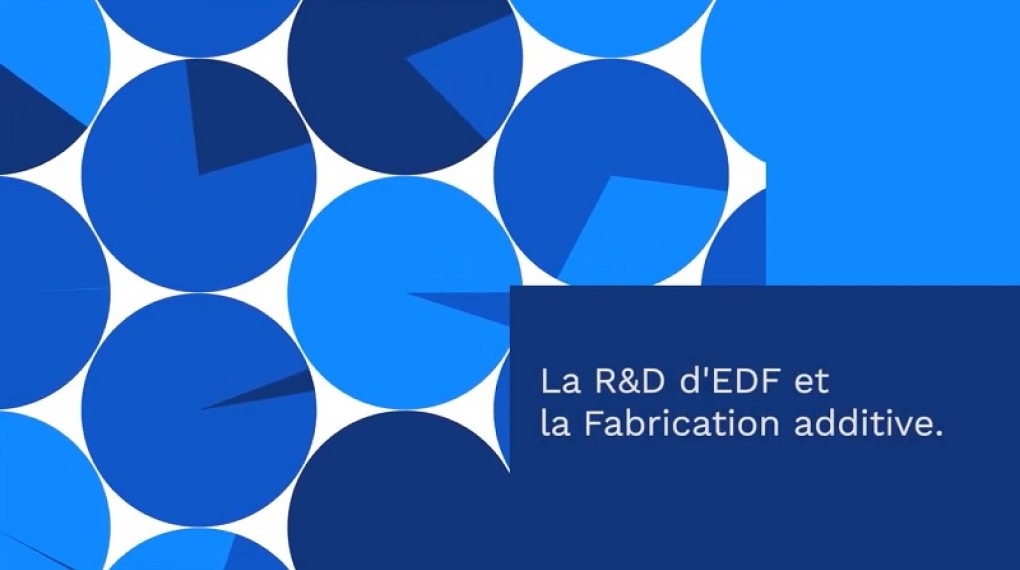
Votre navigateur ne prend pas en compte le javascript.
Pour vous permettre d'accéder à l'information, nous vous proposons de consulter la vidéo dans un nouvel onglet.
Une révolution des modes de production
Ajouter la matière plutôt que la soustraire… qu'est-ce-que cela change au fond ? Cette mise en forme progressive évite ou réduit de nombreuses opérations intermédiaires souvent longues et coûteuses dans les procédés classiques comme la fabrication des moules, l'assemblage des pièces, l'usinage final… Elle garantit en outre une homogénéité chimique, métallurgique et mécanique des pièces fabriquées.
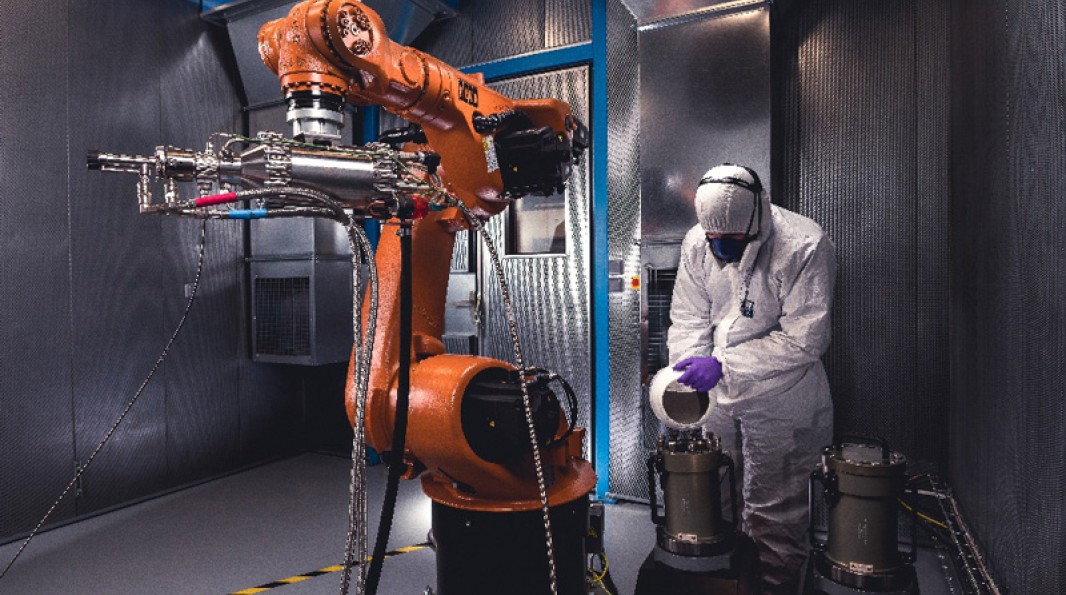
C'est surtout une vraie rupture dans le processus d'approvisionnement. Avec la fabrication additive, on ne stocke plus que de la matière sous forme de poudre ou de fils métalliques… et des plans en 3D, rassemblés dans un catalogue digital, à partir duquel les pièces sont fabriquées directement à la demande. Une solution à la gestion de l'obsolescence des pièces de rechange, comme le souligne Yang Shen. « La plupart de nos installations ont été construites dans les années 70/80. Lorsqu'une pièce doit être remplacée, il arrive que le fabricant n'existe plus, ou ne puisse pas la refabriquer. Avec la fabrication additive, il suffit de récupérer la pièce en l'état, d'en faire un scan 3D pour obtenir un plan numérique, pour la refabriquer directement. Résultats : des délais et des coûts de fabrication réduits, et une sûreté accrue des installations ».
Dernier atout: les opportunités d'optimisation de la conception des pièces. « En s'affranchissant des contraintes d'usinage et d'assemblage, on peut mettre de la matière uniquement là où on en a besoin, ce qui permet d'alléger la structure et diminuer le coût d'approvisionnement », explique le chercheur.
Quels enjeux pour EDF ?
Ils sont de plusieurs ordres. Il s'agit dans un premier temps d'utiliser l'ensemble des compétences en métallurgie, mécanique, chimie, corrosion, simulation numérique pour s'approprier ces technologies afin d'en comprendre les performances et les limites, puis de lever les verrous technologiques liés à la qualité de fabrication et au comportement en service. Enfin, il faudra également accompagner la filière vers la normalisation et la standardisation.
Au niveau de la R&D, cette ambition s'est traduite depuis quelques années par la mise en place d'une équipe de chercheurs chargée d'évaluer l'apport de ces nouveaux procédés dans les activités du groupe. « Nous sommes là pour démontrer qu'ils sont applicables pour la fabrication et la réparation de nos composants, poursuit le chercheur. Nous avons pour cela sollicité à la fois le tissu industriel et des partenaires académiques pour proposer des solutions innovantes permettant de pallier les limites des techniques standard. D'importants investissements ont été réalisés, avec notamment la construction de deux laboratoires dédiés aux procédés Cold Spray (sur le site des Renardières) et WAAM (sur le site de Chatou) en plus de la mobilisation des moyens de simulation et des laboratoires d'expertises dont nous disposions déjà. »
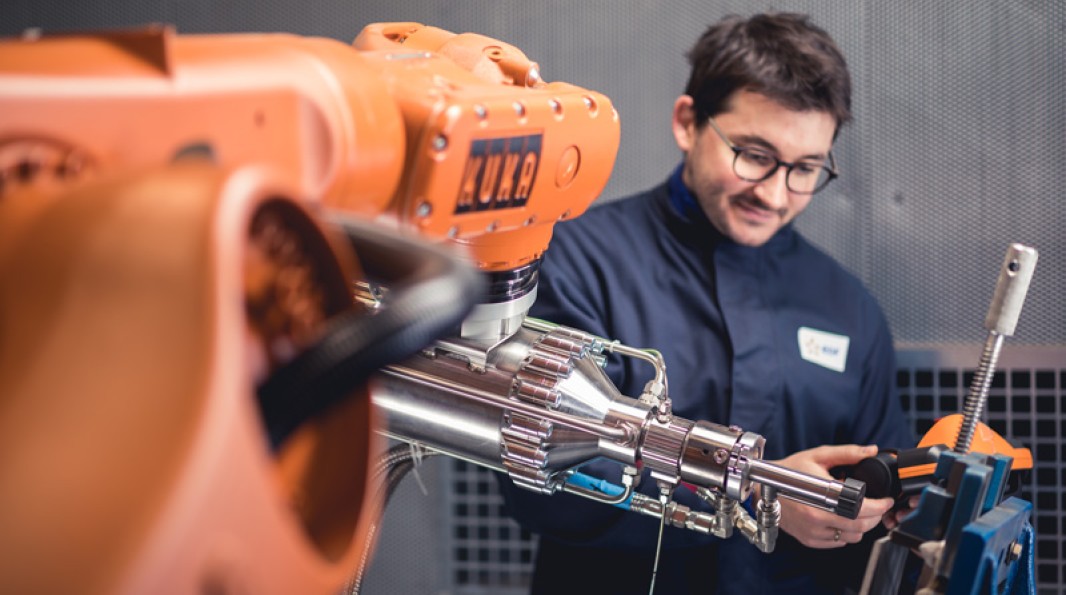
Une palette de procédés pour des applications diverses
Plusieurs applications ont d'ores et déjà été envisagées dans les différents parcs de production. « Pour le parc nucléaire, nous travaillons pour l'instant sur la fabrication de pièces de rechange de robinetterie par le procédé fonderie rapide ou la fusion laser sur lit de poudres (Selective Laser Melting ou SLM). Nous évaluons également la performance et les limites des procédés Cold Spray (lien vers vidéo Cold spray) et Laser Cladding pour la réparation des composants (échangeurs, compensateurs, tubes…) ». Pour le parc hydraulique, ce sont des grosses pièces de turbine pouvant aller jusqu'à dix mètres de long qui sont en cours de fabrication à l'aide du procédé WAAM (Wire Arc Additive Manufacturing) (lien vers vidéo WAAM)
« Nous avons avancé sur le développement des procédés, le prototypage des pièces et les essais, et entamons les phases de qualification et de déploiement. Et tout ça en à peine trois ans… » se félicite Yang Shen. L'étape de la qualification est fondamentale. Elle vise à garantir que la qualité des pièces produites est conforme aux exigences réglementaires. « Nous avons commencé par des pièces ayant peu d‘exigences réglementaires. Cela nous permettra d'aller ensuite vers des pièces plus exigeantes en termes de sûreté, comme les équipements sous pression nucléaire », confie Yang Shen.
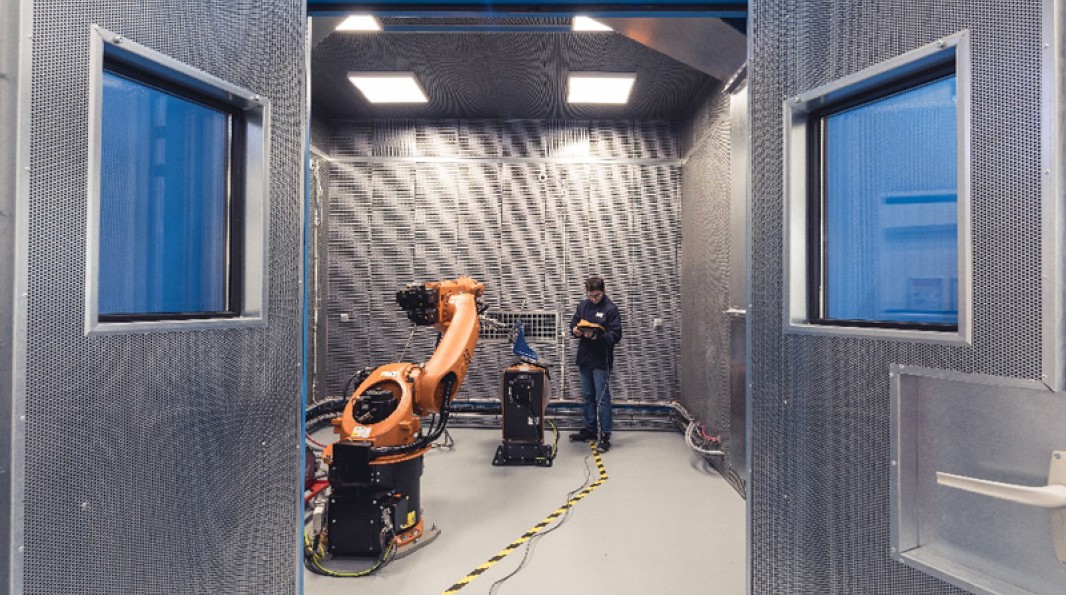
Au cœur de l'usine du futur
Et le jeune pilote ne cache pas son enthousiasme. « La fabrication additive est au cœur de l'usine 4.0. Nous sommes dans une phase de découverte extrêmement stimulante. Les procédés sont en pleine transformation et de nouvelles idées émergent tous les jours. C'est une vraie rupture technologique, et une véritable aventure humaine, avec des projets à la fois très innovants et très applicatifs, où il faut faire preuve d'une grande créativité. C'est passionnant ! »
Pourquoi parle-t-on d'usine 4.0 ?
Ce terme fait référence aux différentes révolutions industrielles. La première date des années 1860-1870 avec l'apparition des premières usines qui tournaient au charbon et la mise au point de la machine à vapeur. La deuxième révolution, en 1920, a été l'introduction de l'électricité. La troisième remonte aux années 60, avec l'arrivée de l'électronique et de l'informatique. Enfin, nous vivons actuellement la quatrième révolution industrielle, celle de l'usine 4.0. Une usine « intelligente », qui se caractérise par des interactions entre des machines et des systèmes répartis au sein des sites de production. La fabrication additive, en permettant de fabriquer à la demande, de façon individualisée et diversifiée, à partir de plans 3D numériques, s'intègre dans ce nouvel environnement.
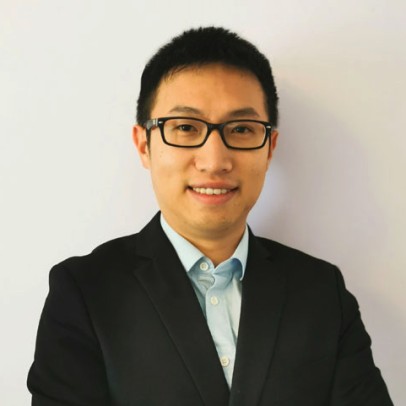
Portrait de Yang SHEN
Après plusieurs années à la direction industrielle d'EDF, Yang Shen pilote le projet Procédés de Fabrication Innovants* à la R&D d'EDF depuis 2019. Ce jeune ingénieur de 36 ans met son esprit fédérateur, son enthousiasme communicatif et ses solides compétences scientifiques et techniques au service d'un projet ambitieux : lever les verrous technologiques pour développer les procédés de fabrication additive au sein des différents métiers d'EDF. Et contribuer ainsi à positionner le groupe comme un acteur majeur de ce secteur en plein essor.
Des procédés de fabrication innovants pour bâtir l'usine du futur
Après avoir effectué sa formation supérieure en Chine avec un Bachelor en génie industriel axé sur l'optimisation de la qualité et de la productivité de la chaine logistique des entreprises, Yang Shen complète sa formation à l'Ecole des Mines de Nancy qui fait de lui un ingénieur généraliste, avec une spécialité en sciences des matériaux. Il décide alors de poursuivre ce cursus par une thèse menée avec le CEA, Framatome et le Centre des matériaux des Mines Paristech. Objectif : étudier le comportement mécanique des matériaux destinés à la construction du réacteur expérimental Jules Horowitz. Ce sera son premier contact avec le monde du nucléaire, qu'il ne quittera plus !
Découverte du monde industriel
Son doctorat en poche, il se forge une première expérience dans l'industrie chez Mitsubishi Heavy Industry et Comex Nucléaire, en tant qu'ingénieur calcul pour le dimensionnement des générateurs de vapeur destinés aux réacteurs français, avant de rejoindre EDF deux ans plus tard. « Ce qui m'a attiré ? Le contenu technique du poste, les possibilités d'évolution et la dimension internationale d'un groupe comme EDF. »
C'est à la direction industrielle qu'il fait ses premières armes, plus précisément au département Matériaux et Chimie où il prend en charge plusieurs dossiers sur la durée de vie des réacteurs nucléaires. Il élabore notamment un programme de surveillance des effets d'irradiation, étudie l'endommagement des pompes du circuit primaires, et prend en charge les expertises nécessaires au redémarrage d'un réacteur après arrêt fortuit. « Il arrive que certaines pièces ayant un impact sur la sûreté du réacteur soient endommagées en fonctionnement. Il faut alors rapidement les déposer, les expertiser en laboratoire pour comprendre l'origine de l'endommagement avant de les remplacer pour pouvoir redémarrer le réacteur », explique le jeune ingénieur. Ce travail en équipe, aussi bien en interne avec ses collègues de l'ingénierie et de la production qu'avec des experts externes, lui permet de se constituer un solide réseau et le dote d'une vision transverse précieuse des métiers de la production d'électricité.
Après l'ingénierie, la recherche
En 2019, il arrive à la R&D. Nouvel environnement, nouveau défi ! Et surtout, une belle occasion de marier son goût pour la technique et son appétence pour l'innovation technologique et la coordination d'équipe, autour d'un projet scientifique et industriel fédérateur : les procédés de fabrication innovants (PROFI) … et parmi eux, la fabrication additive (lien vers article lead de la pépite). « Mes connaissances en métallurgie et en mécanique, mon expérience en matière de conception et de pilotage et ma bonne compréhension des contraintes liées à la maintenance du parc de production, me servent pleinement aujourd'hui pour coordonner ce projet passionnant. La fabrication additive est au cœur de l'usine 4.0. On a vraiment le sentiment d'être en train de bâtir le futur ! s'enthousiasme Yang Shen. En passant de l'ingénierie à la R&D, je ne suis plus un « client » de la R&D mais au contraire là pour répondre aux besoins des métiers du groupe ». Un changement de posture qu'il apprécie tout particulièrement. « Il faut vraiment être à l'écoute, pour trouver les applications possibles de ces procédés dans les différents parcs. Nous travaillons déjà pour le parc nucléaire, le thermique, l'hydraulique, et nous sommes aussi en contact avec les parcs éoliens et solaire et le nouveau nucléaire. C'est très ouvert ».
Réussir la démonstration de la fabrication des pièces pour convaincre
Une fois le cas d'usage identifié, le travail est loin d'être terminé : il y a l'optimisation et la modélisation du design, le choix du matériau et du procédé, l'optimisation des paramètres de fabrication par la simulation numérique, la fabrication et le parachèvement, les tests de prototypage, puis le déploiement sur site, sans oublier la qualification des pièces. « L'identification des cas d'usage et la qualification sont les principaux freins aujourd'hui et ce sont les étapes sur lesquelles nous concentrons nos efforts. Il y a un important travail à faire à la fois pour mieux faire connaître ces procédés et pour garantir la qualité des pièces obtenues. Le premier réflexe est souvent le recours aux procédés classiques, alors que la fabrication additive permet de réduire le délai de fabrication d'un facteur 3 ou 4 ! Mais plus nous aurons d'exemples d'applications menés à bien avec nos centres d'ingénierie et nos sous-traitants, plus nous convaincrons ! »