Le parc nucléaire à l'heure de la fabrication additive
Cédric Pokor travaille à l'Unité Technique Opérationnelle (UTO) de la Direction de la Production Nucléaire (DPN) et il apporte son expertise technique aux différents centres nucléaires de production d'électricité (CNPE). Spécialiste des fabrications innovantes, il nous en dit plus sur l'intégration de la fabrication additive au parc nucléaire.
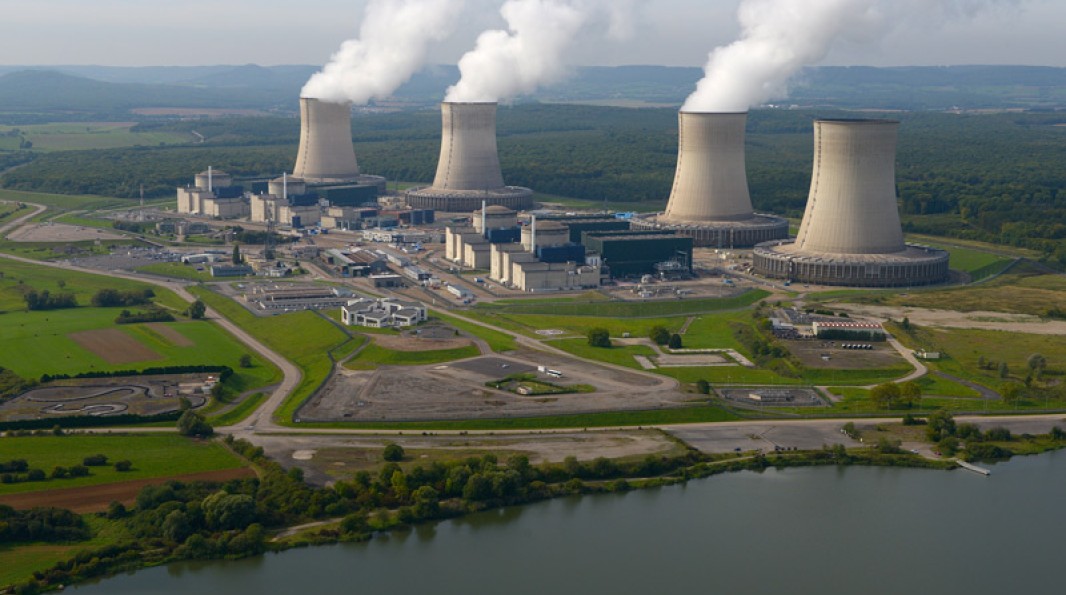
Quelles sont les attentes du parc nucléaire vis-à-vis de la fabrication additive ?
Pour ce qui est du parc actuel, la fabrication additive sera principalement utilisée pour traiter des problèmes d'obsolescence. Grâce à elle, nous reproduirons des pièces que le tissu industriel n'est plus en mesure de réaliser. En effet, le parc nucléaire a été construit il y a une quarantaine d'années et beaucoup de fabricants n'existent plus. L'idée est donc d'effectuer des scans 3D des pièces usagées pour ensuite les reconstituer par fabrication additive. Dans le cadre du parc futur, et notamment des EPR 2, l'idée serait plutôt d'optimiser les designs des matériels et de les fabriquer en utilisant la fabrication additive, qui permet de créer des géométries beaucoup plus libres que par les techniques classiques. En optimisant le design et la matière, on optimise le coût car la matière est chère, mais nous améliorons aussi les échanges thermiques ou encore la circulation des fluides. Grâce à la fabrication additive, nous espérons donc non seulement un meilleur rendement mais aussi un meilleur fonctionnement.
Où en êtes-vous dans l'intégration de cette technologie ?
Nous nous appuyons beaucoup sur le projet PROFI de la R & D d'EDF qui vise à identifier les avantages et les limites de la fabrication additive. Nous ne sommes pas encore entrés dans une phase industrielle. Nous essayons donc de comparer les méthodes de fabrication classiques et additives. Compte tenu des exigences de sûreté propres au domaine du nucléaire, il est impératif que ces pièces produites en fabrication additive présentent des caractéristiques mécaniques au moins aussi bonnes que celles conçues de façon traditionnelle.
Avez-vous engagé des projets concrets ?
Oui, nous nous intéressons au cas par cas aux pièces qui deviennent obsolètes. Nous avons par exemple utilisé la fabrication additive il y a quelques mois pour reproduire une arcade de vanne qui a cédé sur le site de Blayais. Nous avons en réalité employé la fabrication additive de manière détournée. Au lieu de produire directement la pièce, nous avons fabriqué le moule qui a permis une production par fonderie classique ! N'oublions pas que nous sommes dans le nucléaire et que la sécurité est primordiale. D'ailleurs, nous n'intervenons que sur des pièces situées dans des circuits auxiliaires des centrales et non sur les installations du circuit primaire ou des zones nucléaires elles-mêmes. C'est le cas par exemple d'un obturateur de robinet du site de Belleville-sur-Loire qui était rouillé et que nous avons remplacé par une pièce réalisée cette fois ci directement par fabrication additive. La méthode employée était celle du SLM (fabrication sur lit de poudre).
Quelles sont justement les techniques de fabrication additive envisagées dans le cadre du nucléaire ?
Toutes les technologies sont envisagées, mais nous pensons que la fabrication sur lit de poudre est celle qui a le plus d'avenir dans le domaine. Notamment parce qu'elle permet de fabriquer des petites pièces ! Nous nous intéressons aussi au Cold Spray pour réparer des tubes usés. Actuellement, si l'on observe une perte de matière, on coupe le tube sur plusieurs mètres et on le remplace. Demain, lorsque le Cold Spray sera bien développé, on viendra simplement rajouter de la matière sur des points précis comme une sorte de pansement. Il y aura un gain important en termes de coûts, mais surtout en matière de sécurité. Car l'opération sera moins longue et les intervenants moins exposés. Enfin pour ce qui est du WAAM (Wire Arc Additive Manufacturing), nous n'avons pas encore identifié ce qu'il pourrait apporter car il est principalement destiné à la fabrication de pièces massives. Pour ce type de matériel, nous privilégions la maintenance car remplacer un robinet de plusieurs tonnes est extrêmement compliqué.
Quelles sont les prochaines étapes pour intégrer la fabrication additive au domaine du nucléaire ?
Dans les trois années qui arrivent, nous allons travailler sur l'introduction de différents paramètres de fabrication additive dans les codes du type RCC-M (Source Autorité de sûreté nucléaire : outil industriel qui peut être utilisé pour répondre aux exigences de la réglementation). On retrouve dans ces codes la fonderie, le moulage, l'usinage mais pas encore la fabrication additive. Une fois que cela sera fait, nous pourrons nous montrer plus réactifs dans la fabrication ! A plus long terme, à horizon 2030, nous travaillerons sur l'intégration de pièces réalisées par fabrication additive aux centrales nouvelle génération. Grâce à cette technologie, nous espérons améliorer certaines pièces.
Existe-t-il des verrous à lever ?
Une des principales inconnues réside dans la contrôlabilité des pièces. Dans le nucléaire, il est essentiel de réaliser des contrôles non destructifs…C'est-à-dire que nous allons périodiquement vérifier l'état d'une tuyauterie par exemple pour s'assurer qu'il n'y a pas de fissure. Pour les pièces de fonderie classiques, il existe des techniques éprouvées telles que la magnétoscopie, les ultrasons ou les courants de Foucault. Mais qu'en sera-t-il pour les pièces réalisées en fabrication additive ? Ce sont des interrogations et des pistes de travail explorées par la R&D d'EDF mais aussi par l'ingénierie. Ils essayent d'adapter ces contrôles non destructifs à la fabrication additive voire d'en développer de nouveaux.
Mais les principaux verrous à lever sont en réalité plus de nature psychologique à mon avis. Le domaine du nucléaire est par essence très conservateur. Il n'est pas facile d'y introduire de nouvelles techniques de fabrication. Lorsqu'on explique que beaucoup de pièces d'aéronautique sont aujourd'hui fabriquées avec cette méthode, le regard change. On a toujours en tête l'image de l'imprimante 3D, mais les nouvelles techniques d'impression métalliques n'ont plus rien à voir !
Fabrication additive : quels emplois pour le parc hydraulique ?
Fabrication additive et parcs hydrauliques sont-ils compatibles ? Éléments de réponse avec Pierre Maruzewski, pilote national du déploiement de la fabrication additive chez EDF Hydro.
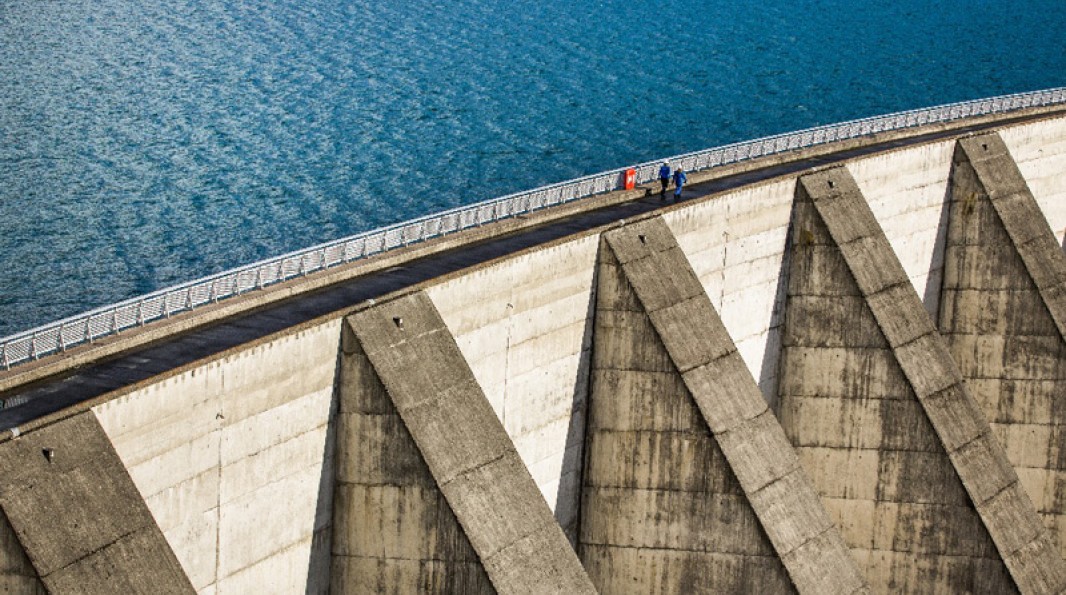
À quelles problématiques vient répondre la fabrication additive ?
Cette technologie est complémentaire de la fabrication traditionnelle dite soustractive (forgeage/moulage). L'enjeu principal pour nous est de diminuer les délais de fabrication des pièces détachées afin de réduire significativement les coûts d'indisponibilité de nos groupes hydro-électriques. Plutôt que de produire des petites pièces en série, nous envisageons de faire appel aux procédés de fabrication additive pour concevoir des grands composants métalliques tels que les composants d'une turbine ou la turbine elle-même. L'objectif est double : d'une part être en mesure de commander rapidement des pièces de rechange aux fabricants mais aussi être en capacité d'effectuer nous-mêmes des réparations avec ces procédés . L'aspect environnemental est un autre aspect important : en utilisant la fabrication additive, on réduit les déchets de matériaux et tous les autres résidus occasionnés par la fabrication traditionnelle.
Y-a-t-il un procédé en particulier qui vous semble plus adapté à vos besoins ?
Actuellement, nous nous concentrons sur le WAAM ( Wire Arc Additive Manufacturing ) qu'on appelle en français « dépôt de fil métallique ». Il permet à un robot de soudure de réaliser des pièces aux formes complexes dont le savoir-faire n'a parfois pas été conservé. Grâce au WAAM, on peut effectuer une sorte de copier/coller d'une pièce actuelle et en créer une autre si celle-ci est en fin de vie ou usagée.
Pour quels projets envisagez-vous de l'utiliser, et à quelle échéance ?
Avec le Centre d'Ingénierie Hydraulique (CIH) et l'Institut de Soudure, nous allons concevoir, dès 2021, un anneau mobile d'un robinet sphérique d'environ un mètre de diamètre sur 12 centimètres d'épaisseur. En parallèle, notre équipe d'électrotechniciens et la Direction Technique Générale (DTG) dirige un projet avec la société INOVSYS dont la finalité est de réaliser un connecteur de traversée des transformateurs. Cette pièce d'une trentaine de centimètres présente une enveloppe métallique qui est conçue grâce à de la fabrication additive. Le tout premier prototype, réalisé en décembre 2020, sera justement monté sur un banc d'essai de la R&D d'EDF début 2021. Enfin à l'horizon 2024, nous voulons remplacer une turbine construite en 1967 et dont la forme est particulièrement complexe. La reproduire en méthode traditionnelle s'avère difficile et nous souhaitons la fabriquer par la technologie WAAM. Nous serons peut-être les premiers producteurs d'énergie en Europe à recourir à la fabrication additive pour alimenter notre parc de machines hydrauliques.
Comment se passe le développement de cette technologie ?
Nous effectuons des études mécaniques, de soudure ou encore de paramétrage du logiciel. Quand on parle de fabrication additive, on pense toujours à une petite imprimante 3D que l'on peut avoir à la maison. Or, avec le WAAM, il s'agit d'un véritable robot avec une torche de soudure… Il y a de multiples paramètres à régler comme la vitesse du robot, de la soudure, du lâcher de fil. Nous travaillons avec R&D d'EDF pour trouver les bons partenaires, et affiner les caractérisations mécaniques et/ou thermiques des pièces. La R&D dispose d'outils et des compétences pointues qui nous permettent d'envisager l'utilisation de cette technologie dans notre parc hydraulique.
Il ne faut pas oublier qu'EDF est un producteur d'énergie et non un constructeur. En matière de fabrication additive, la plupart des grands turbiniers sont encore en phase d'expérimentation, mais nous devons être prêts, connaître les fondements de cette technologie et des différents procédés existants. Il est fondamental que nous comprenions le processus, notamment pour établir des cahiers des charges complets.